Hard to believe with everything that has happened since we started pushing this endeavor back in September. That we're quickly approaching to constructing the production building on a piece of family owned property.
We entertained the idea of starting out of modified shipping containers, prefabbed buildings/sheds, and even trailers but came to the conclusion that a timber framed building will be more cost effective and beneficial for our goals.
Image of: one of the earlier floor plan designs based off of a shipping containers floor space
Although ground hasn't been broken fully for the building, the plan will be to get an insulated slab foundation with radiant floor heating set and placed with multiple floor drains and connections for future alternative uses.
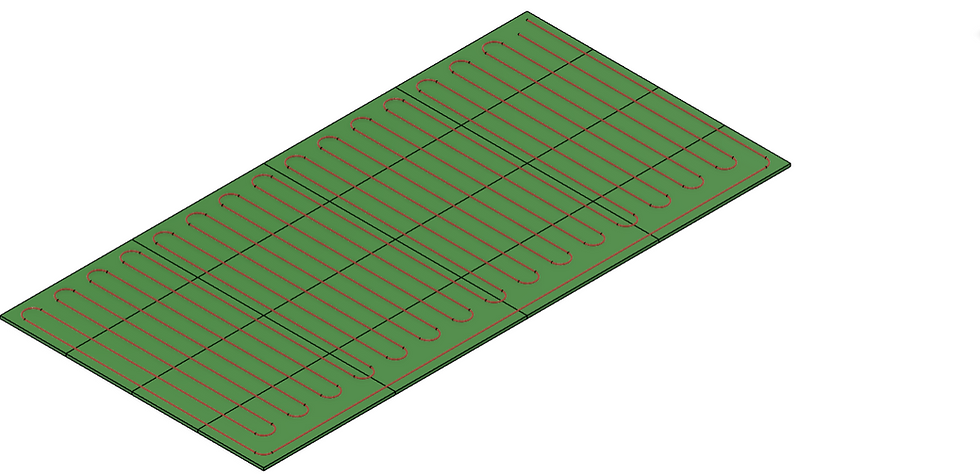
Image of: (Left) Foam insulation and PEX tubing layout that will be placed below and inside the concrete slab foundation, (Right) The resultant concrete slab
End goal of the business is to have a net zero or negative energy consumption from the grid as well as have a sustainable usage of all components that are used to produce our beverages that would mean in future practices we plan to have our own apiary, sugar farm, have a means of our own clean water supplies.
While aiming for our goals we've been actively participating in events that help with getting grants from USDA as well as for green business practices as mentioned from an event we attended with Solar Holler. Simultaneously or after we get our foundation set we will be working on getting as man grants as possible to help finish establishing the building.
In the meantime well make do by producing a building that is planned to be solar powered, geothermally heated, and well insulated for a first production site.
Through this process we started to design the building in CAD software to create a visual aid as well as help create a list of building materials and costs to better estimate the overall cost of the building. The model was also made to be able to be scaled so that it can generate different material totals and models so that a new estimate can be made based upon different floor plan sizes.
Images of: various models generated through the CAD software
Since spring we've been slowly working on breaking ground and determining where on the property to place the building. After the location was roughly determined we created a simple 2x4 frame that we can stake into the ground to represent the building site as well as to begin taking measurements on what's needed to get the ground to grade. We initially started with a simple framing equipment to get to level but quickly determined that a laser leveler is needed to get the accuracy we desired. Resulting in the purchase of a outdoor self balancing laser level and surveying kit.
Our next steps in the process will be to find past used electrical lines and mark them to use for a metered sub panel for the workshop as well as a similar process with the water line mark them for future use making an offshoot to use to supply metered water for the building. after marking those, well continue to make the building grounds to grade and dig the channels for the water lines , electrical lines, and for the perimeter of the foundation to make either a monolithic foundation slab or a floating slab with a perimeter foundation.
コメント